What is the difference between the magnetic latching type and electrical holding type vacuum contactor?
Vacuum contactors are electrical devices used for controlling electric circuits in various applications, such as motor control, lighting, and power distribution. They are designed to make and break electrical connections in a reliable and efficient manner. Vacuum contactors can be classified into two main types based on their mechanism for holding the contacts closed: magnetic latching type and electrical holding type. Here's an overview of the key differences between these two types:
1. Operating Principle:
- Magnetic Latching Type: In a magnetic latching vacuum contactor, the contacts are held closed using a permanent magnet. When the contactor is energized to close the contacts, the permanent magnet locks them in the closed position. To open the contacts, a separate coil is energized to create a magnetic field that opposes the permanent magnet's field, causing the contacts to release and open.
- Electrical Holding Type: In an electrical holding vacuum contactor, the contacts are held closed by an electromagnetic coil. When the coil is energized, it creates a magnetic field that attracts the contacts together, keeping them closed. To open the contacts, the coil is de-energized, and the magnetic force is removed, allowing the contacts to separate.
2. Energy Efficiency:
- Magnetic Latching Type: Magnetic latching contactors tend to be more energy-efficient than electrical holding contactors because they only require energy during the brief periods when the contacts are being opened or closed. The permanent magnet holds the contacts in place without the need for continuous electrical power.
- Electrical Holding Type: Electrical holding contactors require a continuous supply of electrical power to maintain the contacts in the closed position. This can result in higher energy consumption, especially in applications where the contacts are closed for extended periods.
3. Noise and Heat Generation:
- Magnetic Latching Type: Magnetic latching contactors are often quieter and generate less heat compared to electrical holding contactors because they do not require continuous energization of the holding coil.
- Electrical Holding Type: Electrical holding contactors can produce more noise and heat due to the constant energization of the holding coil.
4. Response Time:
- Magnetic Latching Type: Magnetic latching contactors typically have a faster response time because they rely on the rapid reversal of magnetic fields to open and close the contacts.
- Electrical Holding Type: Electrical holding contactors may have a slightly slower response time because the coil must be energized or de-energized to operate the contacts.
5. Operating Frequency:
- Electrical holding type is higher than magnetic latching type.
The choice between magnetic latching and electrical holding vacuum contactors depends on the specific requirements of the application, including energy efficiency, noise considerations, and response time. Each type has its advantages and disadvantages, and the selection should be based on the needs of the electrical circuit or system being controlled.
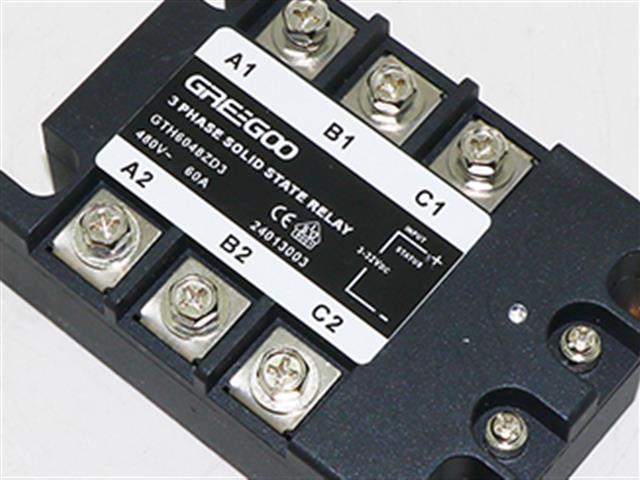
Solid-state relay parameter terms explanation in English.
Parameters terms explanation of SSR
Read More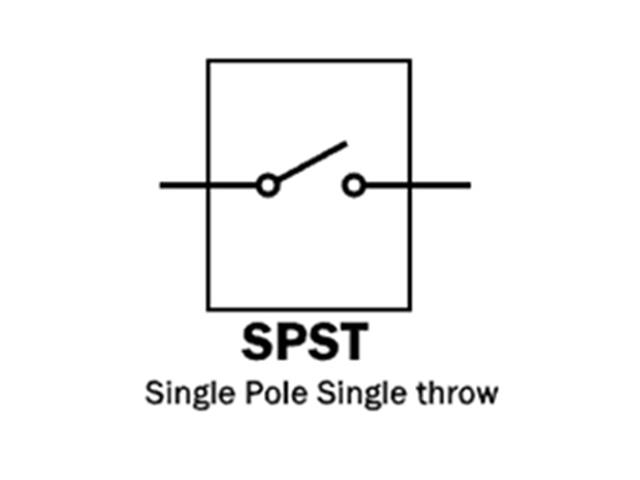
Differences Between Vacuum Relay, SPST-NC, STST-NO, SPDT, and DPDT Switches
SPST-NC, STST-NO, SPDT, and DPDT vacuum relay
Read More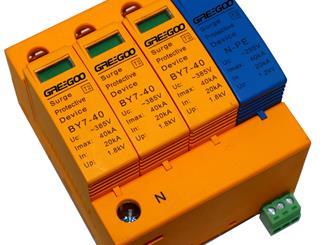
What are the main differences between MOVs and Spark Gaps in SPDs?
An effective surge protection strategy often combines the use of both MOVs and spark gaps, along with other protective devices, to provide comprehensive protection against different levels of power surges.
Read More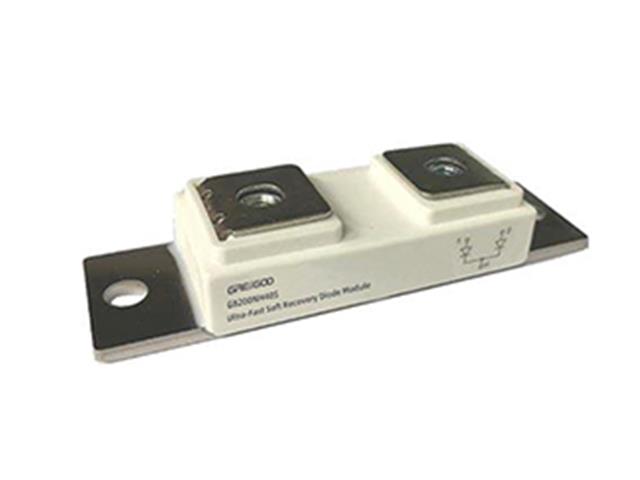
Discover the Greegoo GB Series Fast Recovery Diodes: The Ideal Choice for High-Performance Power Electronics
Unleash the future of power electronics with the Greegoo GB Series—where performance, precision, and flexibility converge.
Read More