Rotating Diode vs. Standard Recovery Diode: Key Difference and Application
The main difference between a rotating diode and a standard recovery diode lies in their applications and performance characteristics:
1. Rotating Diode
- Application: Used in brushless excitation systems of synchronous generators (alternators).
- Function: Converts AC to DC in the exciter rotor circuit to provide field current to the main rotor.
- Characteristics:
- Designed to handle high-speed rotation and mechanical stress.
- High reliability and durability to withstand vibrations and centrifugal forces.
- Typically mounted on the rotating part of the alternator (rotor).
- Works in conjunction with an exciter and main generator to provide a stable DC excitation.
2. Standard Recovery Diode
- Application: General-purpose rectification in power supplies, motor drives, and other electronic circuits.
- Function: Allows current to flow in one direction while blocking it in the other.
- Characteristics:
- Typically has higher reverse recovery time compared to fast recovery or Schottky diodes.
- Used in low to medium-frequency rectification applications.
- Not designed to withstand high mechanical stress or rotation.
Key Differences
Feature | Rotating Diode | Standard Recovery Diode |
---|---|---|
Application | Excitation system of synchronous generators | General rectification in electronics |
Location | Mounted on the rotating part of the machine | Fixed, mounted on a PCB or heat sink |
Durability | Designed for mechanical stress, vibration, and centrifugal force | Standard construction for stationary use |
Speed Consideration | Works in high-speed rotating environments | Used in static applications |
Recovery Time | Fast recovery to improve generator performance | Slower recovery compared to fast recovery diodes |
A rotating diode is a special type of rectifier diode used in the brushless excitation system of synchronous generators (alternators). It is mounted on the rotating part of the machine (rotor) and plays a crucial role in converting AC (alternating current) to DC (direct current) to provide stable excitation to the generator's main field winding.
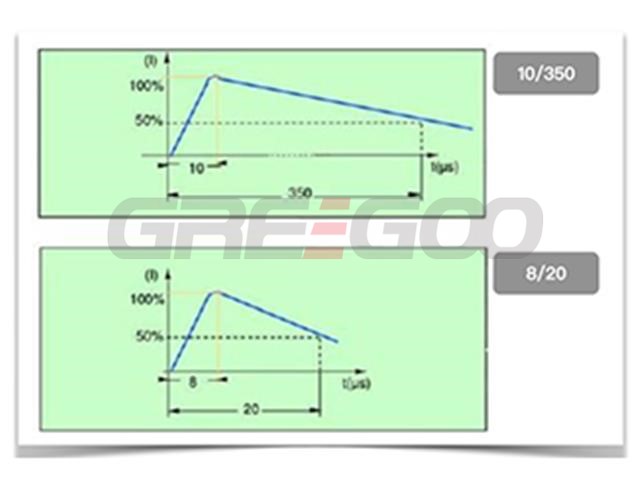
What is the main difference between 8/20μs and 10/350μs in SPD?
8/20μs: Suitable for protection against fast-rising and short-duration surges, such as lightning strikes and rapid switching events.10/350μs: Suitable for protection against slower-rising and longer-duration surges, often associated with power distribution network switching operations and industrial electrical systems.
Read More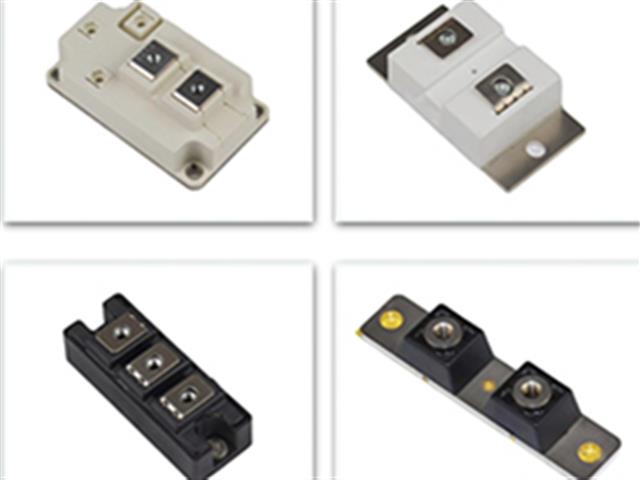
Fast Recovery Epitaxial Diode vs Fast Recovery Diode Module
Key Differences Fast Recovery Epitaxial Diode vs Fast Recovery Diode Module
Read More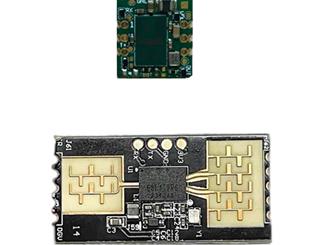
Advanced Low-Power Short-Range Millimeter-Wave Radar Module: Features and Applications
Low Power Short Range Millimeter-Wave Radar Module, the Preferred Choice for Smart Security and Smart Door Lock.
Read More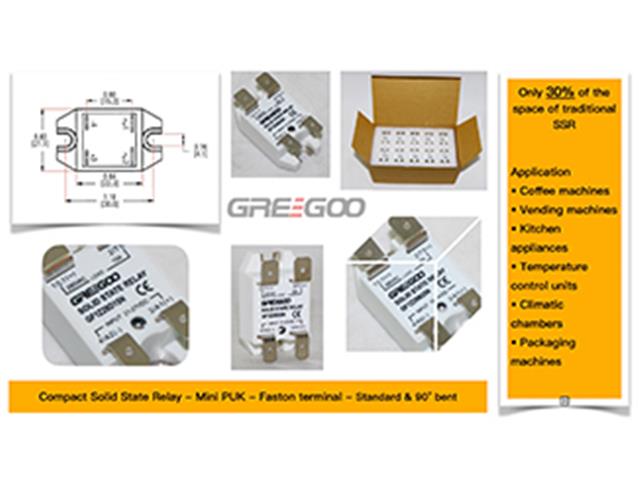
𝑪𝒐𝒎𝒑𝒂𝒄𝒕 𝑺𝒐𝒍𝒊𝒅 𝑺𝒕𝒂𝒕𝒆 𝑹𝒆𝒍𝒂𝒚 - 𝑴𝒊𝒏𝒊 𝑷𝑼𝑲 𝑺𝒐𝒍𝒊𝒅 𝑺𝒕𝒂𝒕𝒆 𝑹𝒆𝒍𝒂𝒚 - 𝑭𝑨𝑺𝑻𝑶𝑵 𝑻𝒆𝒓𝒎𝒊𝒏𝒂𝒍 𝑺𝒐𝒍𝒊𝒅 𝑺𝒕𝒂𝒕𝒆 𝑹𝒆𝒍𝒂𝒚
𝑪𝒐𝒎𝒑𝒂𝒄𝒕 𝑺𝒐𝒍𝒊𝒅 𝑺𝒕𝒂𝒕𝒆 𝑹𝒆𝒍𝒂𝒚 - 𝑴𝒊𝒏𝒊 𝑷𝑼𝑲 𝑺𝒐𝒍𝒊𝒅 𝑺𝒕𝒂𝒕𝒆 𝑹𝒆𝒍𝒂𝒚 - 𝑭𝑨𝑺𝑻𝑶𝑵 𝑻𝒆𝒓𝒎𝒊𝒏𝒂𝒍 𝑺𝒐𝒍𝒊𝒅 𝑺𝒕𝒂𝒕𝒆 𝑹𝒆𝒍𝒂𝒚
Read More